In November 2023, after a three-year journey of efficiently expanding the production of polymer 3D printed parts, the POLYLINE project located at the BMW Additive Manufacturing Park has successfully concluded. The POLYLINE project aims to automate large-scale polymer part additive manufacturing production lines. The work brings together EOS, DyeMansion, BMW and Grenzebach as well as filtration specialist Krumm, software company 3YOURMIND, chemical cleaning specialist Olschner, infrared camera manufacturer Optris, Additive Marking, supply chain service provider WAZP, service companies PROTIQ, Oechsler, STIHL.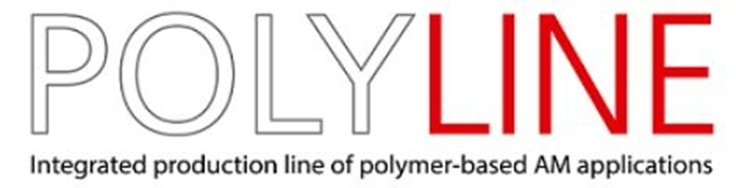
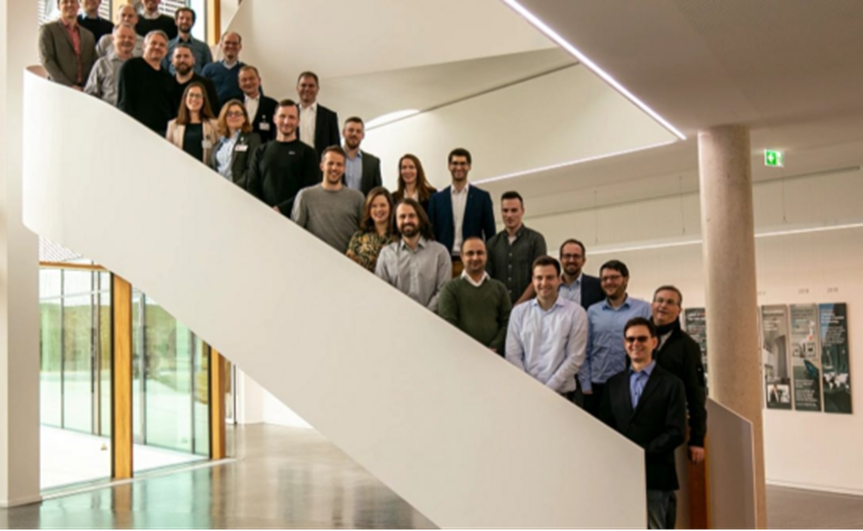
POLYLINE project
Since 3D printing can achieve complex structures and geometries, it is very easy to mass-produce personalized products. However, due to the lack of standards for the entire process chain and the low level of automation in the handling and transportation process, horizontal and vertical additive manufacturing integration of the production line can only be achieved on a limited basis. Other obstacles to large-scale manufacturing include limited monitoring and a lack of transparency throughout the process chain due to discontinuous digital data links at many interfaces, but the potential benefits of integrating additive manufacturing into assembly and series production lines in the automotive industry are huge. , which is why the POLYLINE project was launched.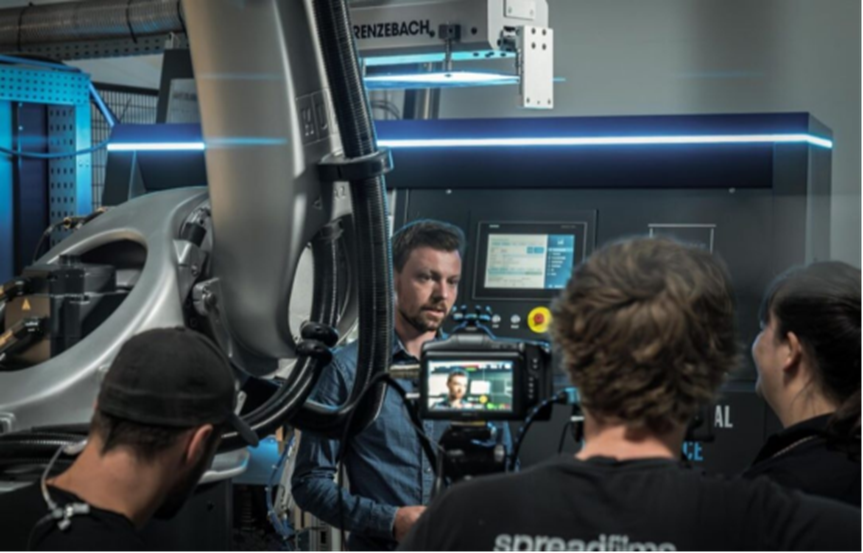
In this project, each partner will make their own contribution to the POLYLINE project: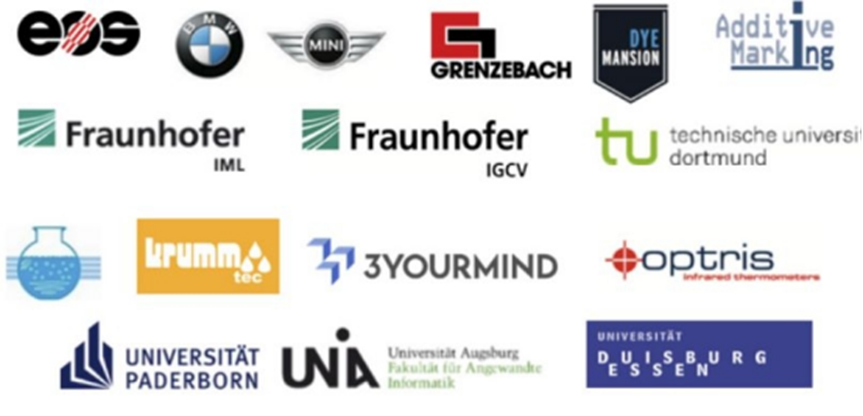
The EOS P 500 system will add real-time monitoring and automatic loading of exchange frames.
Grenzebach, an expert in industrial process automation, will be responsible for the flow and transportation of materials between additive manufacturing processes and help develop automated hardware and software interfaces for these processes.
3YOURMIND is building a data-driven operating model that includes “qualified digital parts inventory, order processing, job and post-processing planning and execution, materials management and quality control.”
Software solutions developer Additive Marking focuses on quality management optimization and resource efficiency.
Post-processing specialist DyeMansion will develop a certified, UV-stabilized automotive color process, leverage its PolyShot Surfaceing (PSS) process to create Industry 4.0-ready cleaning and mechanical surfacing solutions, and contribute its print-to-product platform MES connectivity .
Bernd Olschner GmbH will provide its customer-specific industrial cleaning solutions.
Optris will manufacture fast pyrometers and special thermal imaging cameras suitable for SLS 3D printing of plastics.
Air filtration system manufacturer Krumm-tec will work on upgrading its manual object unpacking process.
Project ended successfully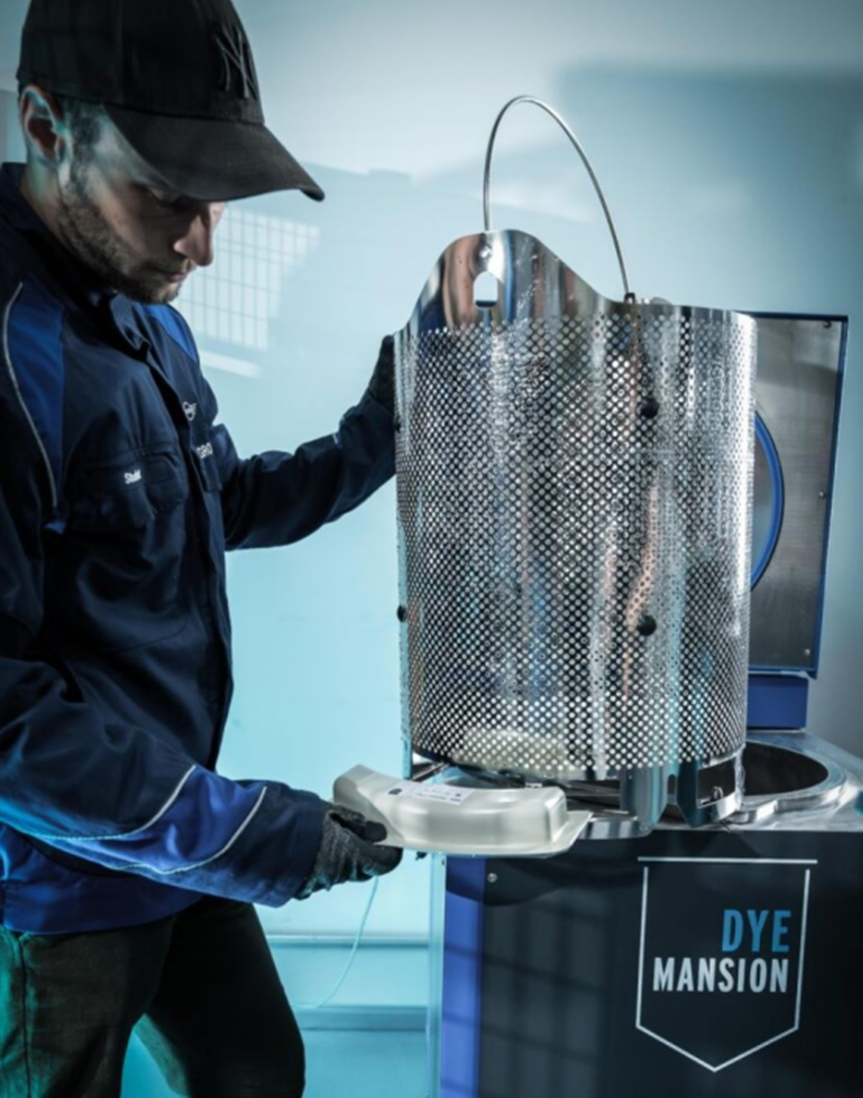
Philipp Kramer, CTO of DyeMansion, said: “The successful POLYLINE project shows that it is possible to build end-to-end automated factories with 3D printing, and this is just the beginning.”
Dr. Blanka Szost-Ouk, Head of Additive Manufacturing, Pre-Development and Planning at the BMW Group, said: “The POLYLINE automated process chain is suitable for next-generation printers and our standard production requirements and, thanks to its standardized interfaces, is a system-independent solution. This is ideal for Scaling additive manufacturing is critical."
Fabian Krauß, Head of Polymer Systems at EOS, said: “We developed this technology at BMW for the automotive industry, and now we can adopt and adapt it to other industries.”
Oliver Elbert, head of additive manufacturing at Grenzebach, said: “The main advantages of automation are increasing the productivity of equipment, reducing equipment downtime and creating a safe working environment for employees.”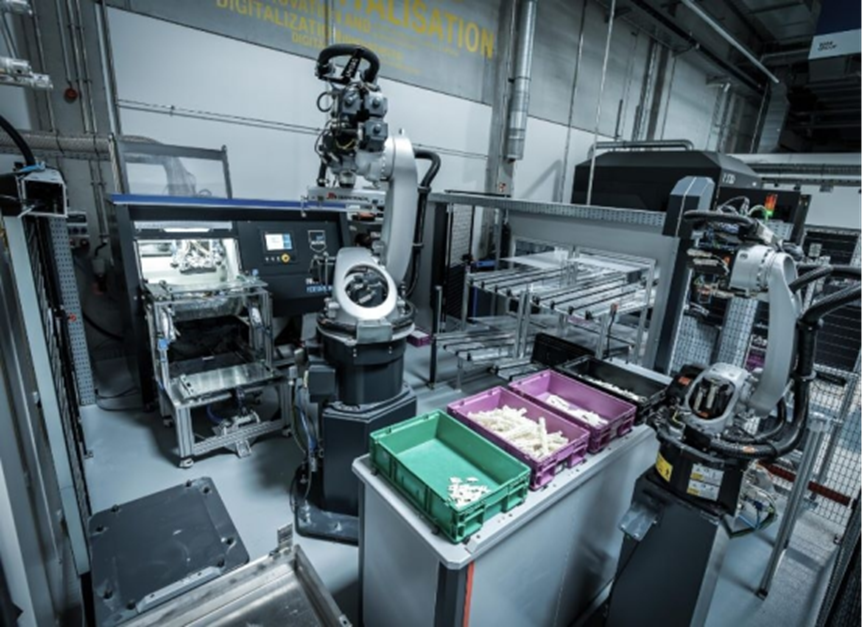
With a German consortium investing approximately $11 million, the project has made significant progress, demonstrating the power of integration, meticulous tracking, collaborative efforts and tight software bindings. Although this process was fraught with many challenges, a viable polymer powder bed fusion production line has now been obtained, which can be further iterated and fine-tuned, opening the door for other entities to collaborate and develop similar solutions. Potential reductions in labor costs and increases in repeatability and reliability present key opportunities and challenges for the additive manufacturing industry.
This is just one part of BMW’s multifaceted approach to automated 3D printing, which sits alongside key projects including one for automated metal 3D printing and another dedicated to sand core printing. The IDAM project, led by the BMW Group, has successfully established two fully automated 3D printing automotive production lines for metal LPBF platforms, artificial intelligence and robotics, significantly enhancing large-scale 3D printing in automotive production. With Loramendi and voxeljet, BMW has also automated the 3D printing of large sand cores for casting cylinder heads for efficient engines.
POLYLINE's hope now lies in the continuity of the alliance, which aims to introduce fully automated production lines to the wider market. This critical integration is a catalyst for cost-effective, widespread part production, marking a major step toward making more products affordably.